01.CCD Detection
Kais has achieved powerful economies of scale through increasing first pass yield (FPY) rate, our production line is equipped with a best-in-class manufacturing monitor system to catch any faulty process exactly where it happens. One such equipment is the Charge-coupled Device.
The CCD solder joint detector is automatic equipment for lithium battery processing, which has the functions of automatic positive and negative pole detection, positive and negative solder joint detection, solder joint defect differentiation, automatic discharge, etc.
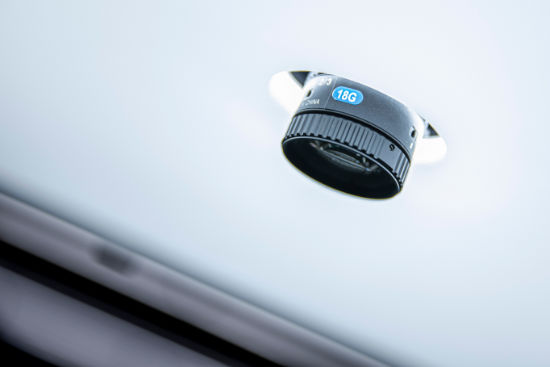
CCD positioning with 0.2mm resolution while insulation paper attachment.
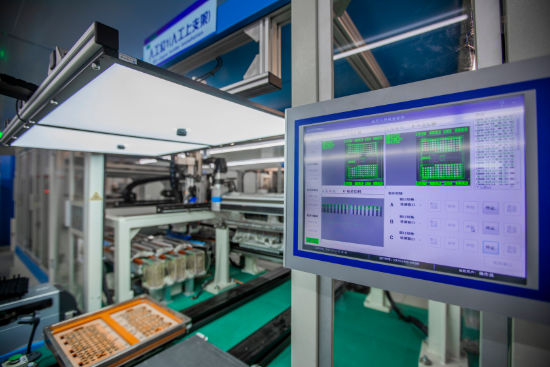
CCD monitoring for cathode/anode polarity during the cell installation process.