MECHANICAL DESIGN
IN THE DETAILS
Lithium-ion battery cells are very delicate products that require very careful handling and meticulous design across every component, even the most minuscule flaw in the pack will steadily build up, breaking cell consistency with each use, and resulting in irreversible damage to the battery health and performance. That’s why Kais takes an overall approach in our design, leveraging our knowledge not only of battery packs but also battery cells, material, and software to design for perfection right down to the tiniest detail.
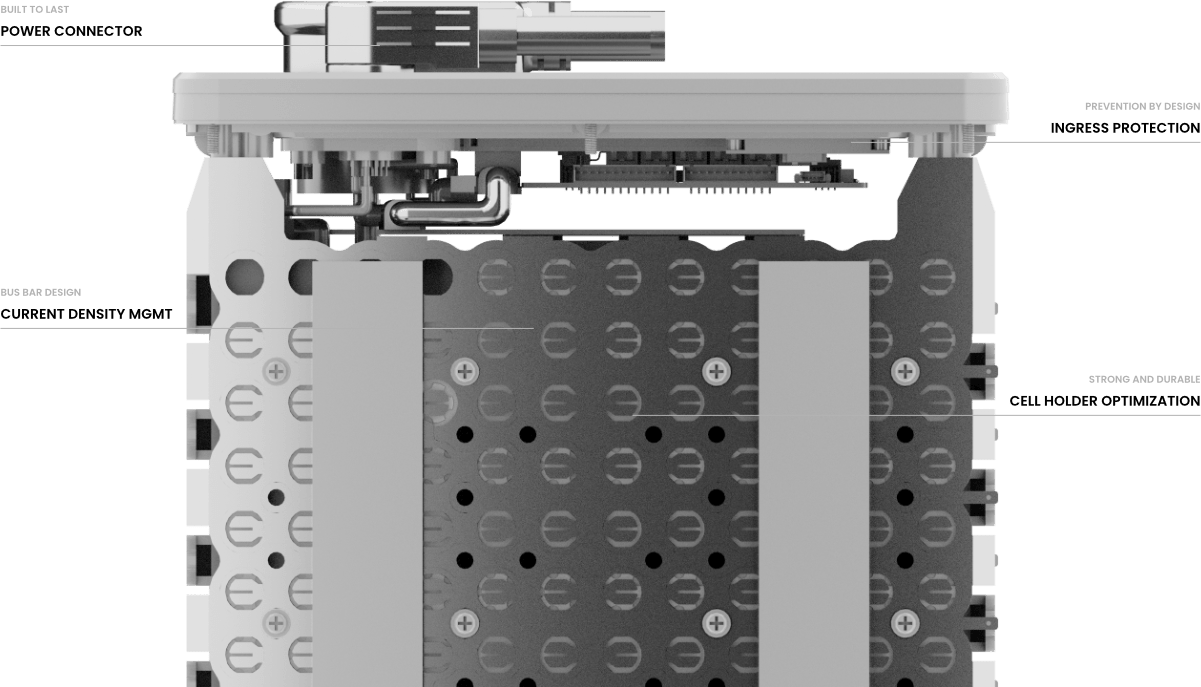